Festo VPPM-8 Bruksanvisning
Festo
Ikke kategorisert
VPPM-8
Les nedenfor 📖 manual på norsk for Festo VPPM-8 (4 sider) i kategorien Ikke kategorisert. Denne guiden var nyttig for 13 personer og ble vurdert med 4.5 stjerner i gjennomsnitt av 2 brukere
Side 1/4
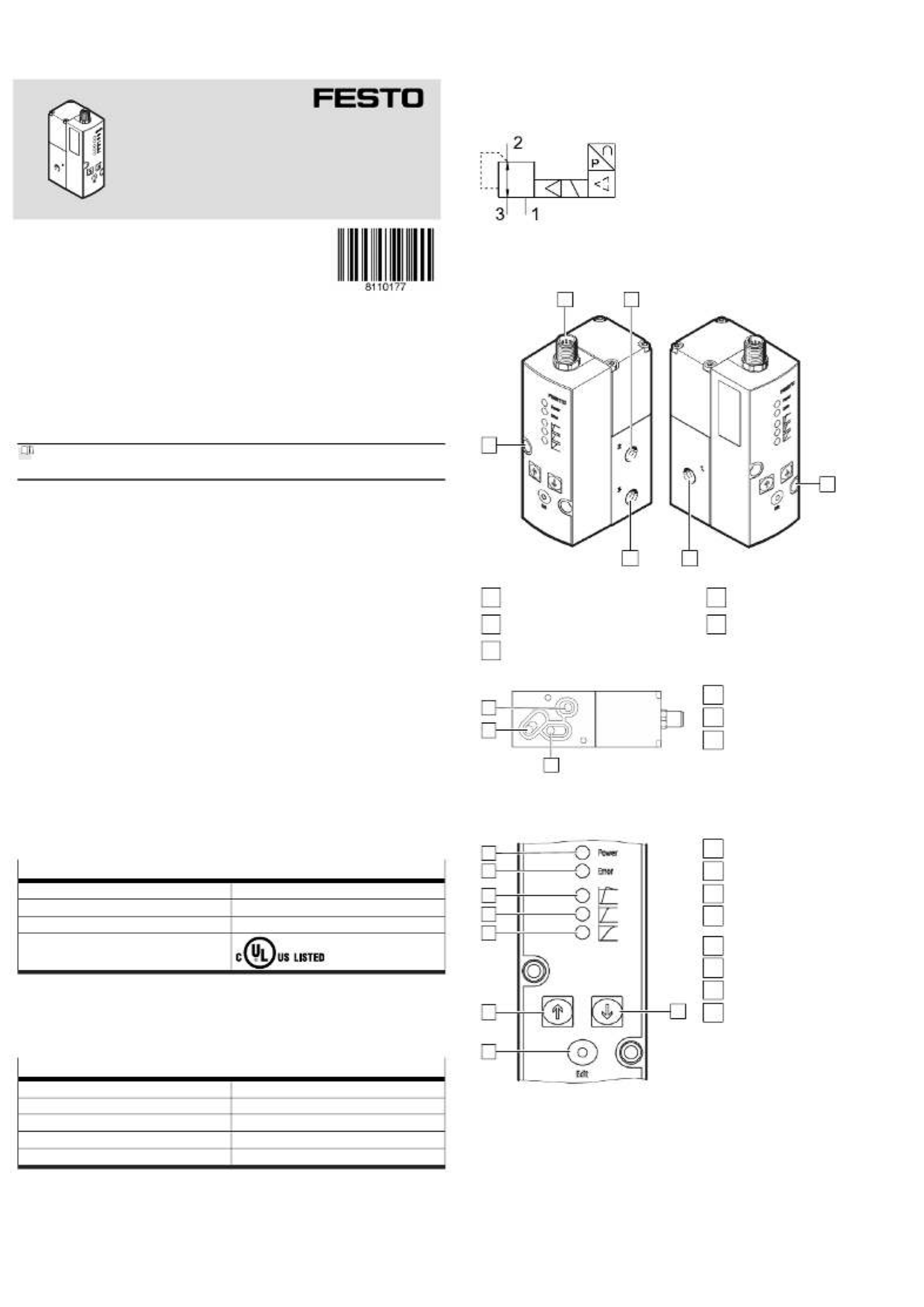
VPPM
Proportional-pressure regulator
Festo SE & Co. KG
Ruiter Straße 82
73734 Esslingen
Deutschland
+49 711 347-0
www.festo.com
Operating instructions
8110177
2021-11g
[8110179]
Translation of the original instructions
© 2021 all rights reserved to Festo SE & Co. KG
1 Applicable Documents
All available documents for the product
è www.festo.com/sp.
2 Safety
2.1 Safety instructions
–Only use the product in its original condition without unauthorised modifica-
tions.
–Only use the product if it is in perfect technical condition.
–Take into account the ambient conditions at the location of use.
–Before working on the product, switch off the power supply and secure it
against being switched on again.
–Store the product in a cool, dry environment protected from UV and corrosion.
Keep storage times short.
2.2 Intended use
The proportional-pressure regulator is intended to regulate a pressure propor-
tional to a specified setpoint value. The product is intended for use in industrial
environments.
2.3 Training of qualified personnel
Work on the product may only be carried out by qualified personnel who can
evaluate the work and detect dangers. The qualified personnel have skills and
experience in dealing with electropneumatic (open-loop) control technology.
2.4 Approvals
In combination with the UL inspection mark on the product, the information in this
section must also be observed in order to comply with the certification conditions
of Underwriters Laboratories Inc. (UL) for USA and Canada.
UL certification information
Product category code QUYX, QUYX7
File number E322346
Considered standards UL 610101, CAN/CSAC22.2 No. 610101
UL mark
Tab. 1: UL certification information
–The unit shall be supplied by a power source which fulfils the requirements
on a limited-energy circuit in accordance to IEC/EN/UL/CSA 61010-1 or on
a Limited Power Source (LPS) in accordance to IEC/EN/UL/CSA 60950-1 or
IEC/EN/UL/CSA 62368-1 or a Class 2 circuit in accordance to NEC or CEC.
Electrical data and ambient conditions
Supply voltage 24 V DC
Max. power VPPM-6, VPPM-8 7 W
Max. power VPPM-12 12 W
Rated pressure up to 1.1 MPa
Max. installation height 2000 m
Tab. 2: Electrical data and ambient conditions
3 Additional information
–Contact the regional Festo contact if you have technical problems
è www.festo.com.
–Accessories and spare parts è www.festo.com/catalogue.
4 Product overview
4.1 Function
The proportional-pressure regulator controls the pressure proportionally to a
specified setpoint value. A built-in pressure sensor records the pressure at the
working port and compares this value with the setpoint value. If there are devia-
tions between the setpoint value and actual values, the proportional-pressure
regulator is actuated until the output pressure has reached the setpoint.
Fig. 1: Pneumatic circuit symbol
4.2 Structure
4.2.1 Product design
1
2 3
5 4
1
Fig. 2: Connections and mounting holes (in-line valve)
1
Through-holes for fastening
2
Electrical connecting plug
3
Working air port (2)
4
Compressed air port (1)
5
Exhaust air port (3)
2
1
3
Fig. 3: Pneumatic ports (sub base
valve)
1
Exhaust air port (3)
2
Working air port (2)
3
Compressed air port (1)
4.2.2 Display and control elements
5
4
3
2
1
8
6
7
Fig. 4: Display and control elements
1
[Edit] key
2
[UP] key
3
Yellow LED: precise control response
4
Yellow LED: universal control response
(factory setting)
5
Yellow LED: fast control response
6
Red LED [error]
7
Green LED [power]
8
[DOWN] key
5 Transport
Store and transport the product in its original packaging. Observe the weight, the
dimensions and the ambient conditions.
6 Assembly
6.1 Mounting clearances
During assembly make sure that there is sufficient space for the cable connection
and the tubing connections. Place the device as close to the consumer as pos-
sible. This leads to better control accuracy and shorter response times.
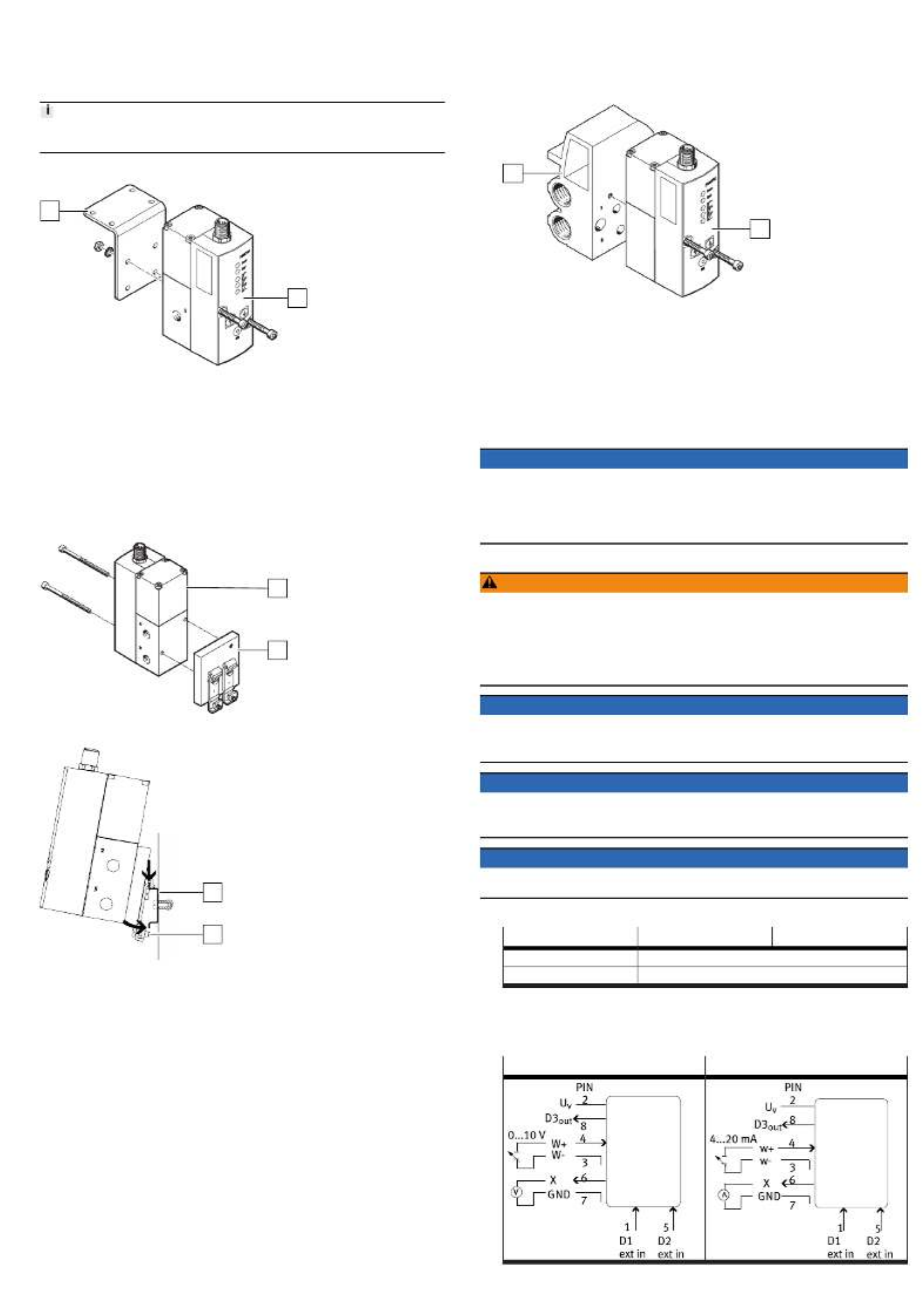
6.2 Wall mounting (in-line valve)
VPPM-6L-... and VPPM-8L-...
• Fasten the VPPM-... [2] with 2 M4 screws. If necessary, use the bracket VAME-
P1-A [1].
–Tightening torque: 1.5 Nm
Only apply a static load to the VPPM-... when mounting the VPPM-... with the
assistance of the bracket.
2
1
VPPM-12L-...
• Fasten the VPPM-… with 2 M5 screws.
–Tightening torque: 2.0 Nm
6.3 H.rail mounting (in-line valve)
VPPM-6L-... and VPPM-8L-...
1. Attach the H-rail adapter VAME-P1-T [2] to the VPPM-... with 2 screws [1].
–Screws: M4 x 65 for VPPM-6L-..., M4 x 77 for VPPM-8L-...
–Tightening torque: 1.5 Nm
2
1
2. Attach the VPPM -... to the H-rail.
2
1
3. Fasten the VPPM-... with the retaining screw [2] of the H-rail adapter.
–Tightening torque: 1.5 Nm
6.4 Manifold block assembly (sub base valve)
VPPM-6F-... and VPPM-8F-...
• Fasten the VPPM-... [2] to the manifold block [1] with 2 screws.
–Screws: M4 x 65 for VPPM-6F-..., M4 x 77 for VPPM-8F-...
–Tightening torque: 1.5 Nm
2
1
7 Installation
7.1 Pneumatic installation (in-line valve)
1. Remove the covers from the supply ports.
2. Connect the compressed air port (1) and the working air port (2) with tubing
è Fig. 2.
3. Fit a silencer at the exhaust air port (3) or install an exhaust air duct è Fig. 2.
Operating medium
NOTICE
Too much residual oil content in the compressed air will reduce the service life of
the valve.
• When using bio-oils (oils that are based on synthetic ester or native ester,
e.g. rapeseed oil methyl ester), the maximum residual oil content of 0.1 mg/m³
must not be exceeded (ISO 8573-1:2010 [–:–:2]).
7.2 Electrical installation
WARNING
Risk of injury due to electric shock.
• For the electrical power supply, use only PELV circuits in accordance with IEC
60204-1/EN 60204-1 (Protective Extra-Low Voltage, PELV).
• Observe the general requirements of IEC 60204-1/EN 60204-1 for PELV circuits.
• Only use voltage sources that ensure a reliable electric separation from the
mains network in accordance with IEC 60204-1/EN 60204-1.
NOTICE
Malfunction due to impaired immunity to interference
Long signal lines reduce the immunity to interference.
• Use the shortest possible signal lines.
NOTICE
• The connector must not be twisted out of the intended position.
• The tightening torque of the M12 plug socket with cable must not exceed
0.5 Nm.
NOTICE
If the Y-connecting cable type NEBV-M12G8-KD-..-M12G5 is connected to CPX I/O
modules, galvanic isolation of the I/O modules will not be guaranteed.
1. Use the rating plate to check which valve variant is involved.
Valve variant VPPM-...-V1... VPPM-...-A4...
Voltage variant 0 … 10 V DC
Current variant 4 … 20 mA
2. Lay the electrical connection cable without crushing, kinking or stretching it.
3. If a shielded electrical connection cable is used, earth the shield at the end of
the cable remote from the valve.
4. Wire the VPPM-... according to the corresponding plug pattern.
VPPM-...-V1... VPPM-...-A4...
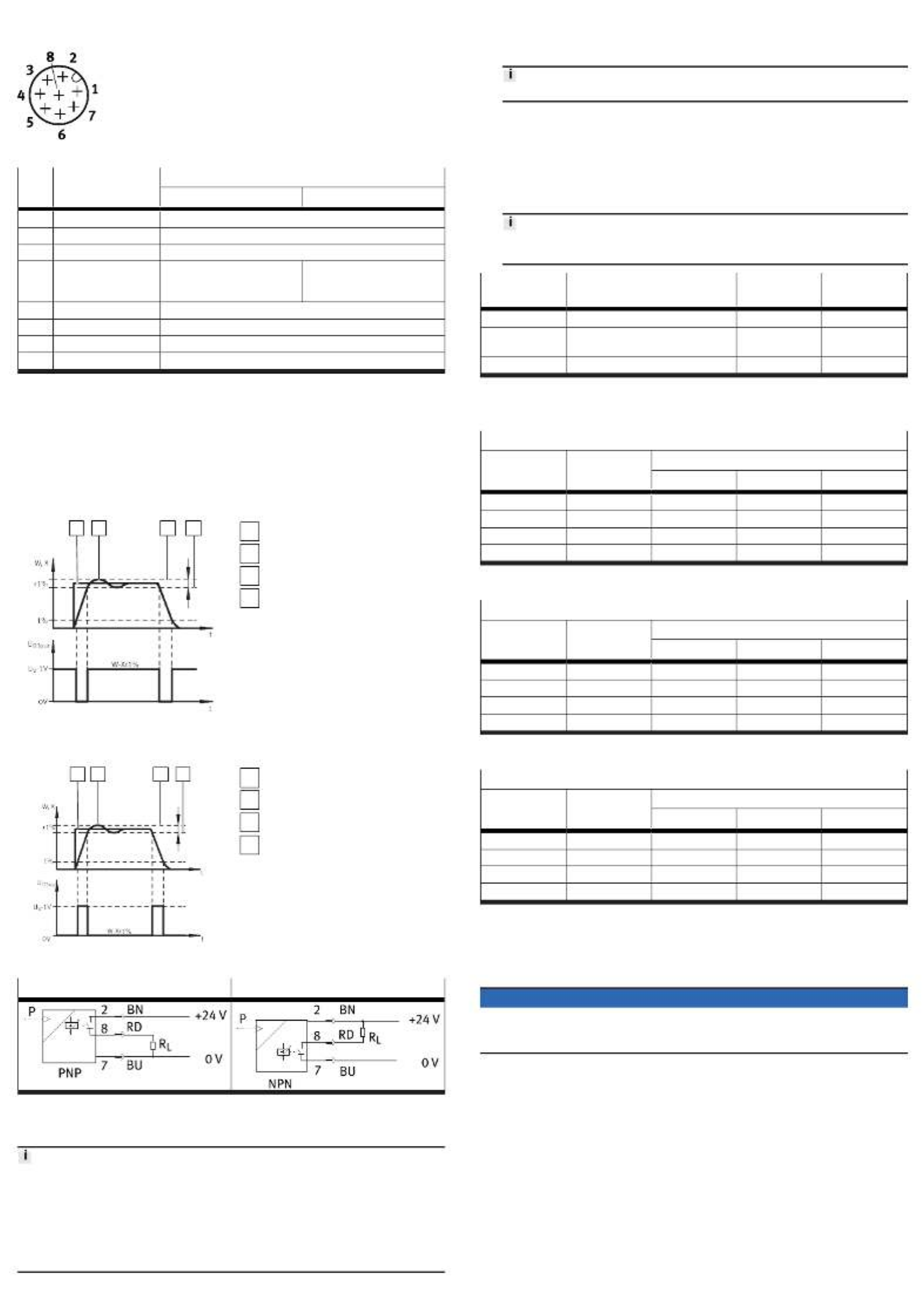
3.
1.
1.
Pin allocation
The pins on the electrical connection are assigned as follows:
Fig. 5: Pin allocation
PIN Wire colour1) Port identifications
VPPM-...-V1... VPPM-...-A4...
1 white (WH) Digital input D1
2 brown (BN) +24 V DC supply voltage
3 green (GN) Analogue input W- (- setpoint value)
4 yellow (YE) Analogue input W+
(+ setpoint value)
0 … 10 V
Analogue input W+
(+ setpoint value)
4 … 20 mA
5 grey (GY) Digital input D2
6 pink (PK) Analogue output X (actual value)
7 blue (BU) GND supply earth
8 red (RD) Digital output D32)
1) With usage of the plug socket with cable as specified in accessories.
2) The hysteresis of the digital comparator output D3 is 0.5% FS.
Tab. 3: Pin allocation
Digital comparator output D3
The “Pressure reached” function permits monitoring of the pressure control func-
tion. The setpoint value is compared with the actual value.
The digital switching output D3 becomes active as soon as the divergence is
£ 0.5% FS and becomes inactive when the divergence 1% FS is exceeded.>
Graph for VPPM-...-...P switching variant
1 2 3 4
Fig. 6: Switching variant VPPM-...-...P
1
Setpoint value
2
Actual value
3
Upper tolerance limit
4
Lower tolerance limit
Graph for VPPM-...-...N switching variant
1 2 3 4
Fig. 7: Switching variant VPPM-...-...N
1
Setpoint value
2
Actual value
3
Upper tolerance limit
4
Lower tolerance limit
Circuit diagram VPPM-...-...P Circuit diagram VPPM-...-...N
Tab. 4: VPPM-... circuit diagrams Switching output
8 Commissioning
• Keep high-frequency radiation away from the VPPM-... in order to avoid
increased tolerances of the outlet pressure.
• The VPPM-... interprets setpoint signals that are less than 1% Full Scale (FS) as
0 V or 4 mA. In this case the working pressure is set to ambient pressure.
• At typical input values below 3.6 mA , the valve detects a cable break and the
last pressure set remains unregulated. Leakage results in a change of pressure
over the long term.
1. Connect the VPPM-... with a setpoint value signal. The VPPM-... has a differen-
tial input. Apply the setpoint signal 0 … 10 V or 4 … 20 mA to contacts 3 and 4.
Apply the lower potential to contact 3 and the higher potential to contact 4.
Contact 3 (– setpoint value) can be connected to contact 7 (GND).
2. Power the VPPM-... with direct current.
–Supply voltage UV = 24 V DC ±10%
Select a parameter set for the regulator.
–Press and hold the [Edit] key for 3 seconds.
–Select a parameter set with the [UP] and [DOWN] keys. The LED of the
selected parameter set lights up.
–Press the [Edit] key to confirm the selection.
The control response of the VPPM-... can also be set by remote control via
digital inputs D1 and D2.
Parameter set Control response Input D1 (PIN
1)
Input D2 (PIN
5)
1 Fast control response 1 (24 V DC) 0 (0 V DC)
2 Factory setting: universal control
response
0 1
3 Precise control response 1 1
Tab. 5: Parameter sets
The following 3 tables show the recommended parameter sets for the different
pneumatic ports:
Parameter sets recommended for VPPM-6...
Tube length1) Open system Output volume in ml
0 … 100 100 … 1000 1000>
0 m 3 3 2 1
1 m 3 3 2 2
3 m 3 3 3 2
³ 5 m 3 3 3 2
1) with inner tubing diameter 6 mm or 8 mm
Tab. 6: Parameter sets recommended for VPPM-6...
Parameter sets recommended for VPPM-8...
Tube length1) Open system Output volume in ml
0 … 500 500 … 2000 2000>
0 m 3 1 2 3
1 m 3 1 2 3
3 m 3 2 3 3
³ 5 m 3 3 3 3
1) with tubing diameter 8 mm or 10 mm
Tab. 7: Parameter sets recommended for VPPM-8...
Parameter sets recommended for VPPM-12L-...
Tube length1) Open system Output volume in ml
0 … 2000 2000 … 10000 10000>
0 m 3 1 2 3
1 m 3 1 2 3
3 m 3 2 3 3
³ 5 m 3 3 3 3
1) with tubing diameter 12 mm or 16 mm
Tab. 8: Parameter sets recommended for VPPM-12L-...
9 Maintenance
9.1 Disassembly
NOTICE
• When switching off the VPPM.-..., first make sure that the setpoint value is set
to 0, then that the supply pressure and finally the supply voltage are switched
off.
Switch off the following energy sources:
–Operating voltage
–Compressed air
2. Disconnect the connections from the device.
3. Remove the device from the mounting surface or H-rail.
9.2 Cleaning
Switch off the following energy sources to clean the outside:
–Operating voltage
–Compressed air
2. Clean the device on the outside with a soft cloth as required.
Produkspesifikasjoner
Merke: | Festo |
Kategori: | Ikke kategorisert |
Modell: | VPPM-8 |
Trenger du hjelp?
Hvis du trenger hjelp med Festo VPPM-8 still et spørsmål nedenfor, og andre brukere vil svare deg
Ikke kategorisert Festo Manualer

31 Mars 2025

31 Mars 2025

31 Mars 2025

31 Mars 2025

31 Mars 2025

31 Mars 2025

31 Mars 2025

31 Mars 2025

31 Mars 2025

31 Mars 2025
Ikke kategorisert Manualer
- Ikke kategorisert MSW
- Ikke kategorisert Stamos
- Ikke kategorisert Teka
- Ikke kategorisert Ulsonix
- Ikke kategorisert Aiwa
- Ikke kategorisert Stamony
- Ikke kategorisert Laica
- Ikke kategorisert Uniprodo
- Ikke kategorisert Miele
- Ikke kategorisert Whirlpool
- Ikke kategorisert ORNO
- Ikke kategorisert Ledlenser
- Ikke kategorisert Fujifilm
- Ikke kategorisert Etna
- Ikke kategorisert Haier
- Ikke kategorisert KitchenAid
- Ikke kategorisert Bauhn
- Ikke kategorisert Insignia
- Ikke kategorisert Royal Catering
- Ikke kategorisert LG
- Ikke kategorisert Bosch
- Ikke kategorisert Jocel
- Ikke kategorisert Power Dynamics
- Ikke kategorisert BEKO
- Ikke kategorisert Exquisit
- Ikke kategorisert Grundig
- Ikke kategorisert Hisense
- Ikke kategorisert Sharp
- Ikke kategorisert D-Link
- Ikke kategorisert Electrolux
- Ikke kategorisert Apc
- Ikke kategorisert Severin
- Ikke kategorisert Café
- Ikke kategorisert Balay
- Ikke kategorisert DeWalt
- Ikke kategorisert Siemens
- Ikke kategorisert Hama
- Ikke kategorisert Petsafe
- Ikke kategorisert Vorago
- Ikke kategorisert Neewer
- Ikke kategorisert Jensen
- Ikke kategorisert Danby
- Ikke kategorisert Bartscher
- Ikke kategorisert Hartke
- Ikke kategorisert Gigabyte
- Ikke kategorisert Smeg
- Ikke kategorisert Gree
- Ikke kategorisert Hoover
- Ikke kategorisert EBERLE
- Ikke kategorisert Hazet
- Ikke kategorisert Fluke
- Ikke kategorisert Philips
- Ikke kategorisert Topeak
- Ikke kategorisert Antari
- Ikke kategorisert Thermex
- Ikke kategorisert TCL
- Ikke kategorisert Russell Hobbs
- Ikke kategorisert Panduit
- Ikke kategorisert IFM
- Ikke kategorisert Avantree
- Ikke kategorisert Hotpoint
- Ikke kategorisert Schwaiger
- Ikke kategorisert Arendo
- Ikke kategorisert Godox
- Ikke kategorisert Megger
- Ikke kategorisert Noxon
- Ikke kategorisert Amica
- Ikke kategorisert Sanus
- Ikke kategorisert Adidas
- Ikke kategorisert Domo
- Ikke kategorisert IKEA
- Ikke kategorisert AEG
- Ikke kategorisert TP Link
- Ikke kategorisert Inventum
- Ikke kategorisert Totolink
- Ikke kategorisert Gamma
- Ikke kategorisert Artusi
- Ikke kategorisert Navitel
- Ikke kategorisert Meridian
- Ikke kategorisert Cecotec
- Ikke kategorisert AeroCool
- Ikke kategorisert Kugoo
- Ikke kategorisert Rikon
- Ikke kategorisert Samsung
- Ikke kategorisert Neff
- Ikke kategorisert Garmin
- Ikke kategorisert Razer
- Ikke kategorisert Teufel
- Ikke kategorisert Noveen
- Ikke kategorisert Fender
- Ikke kategorisert StarTech.com
- Ikke kategorisert Outwell
- Ikke kategorisert Best
- Ikke kategorisert Stihl
- Ikke kategorisert Delonghi
- Ikke kategorisert ZOTAC
- Ikke kategorisert Comfee
- Ikke kategorisert Imarflex
- Ikke kategorisert Edgestar
- Ikke kategorisert Audient
- Ikke kategorisert Kogan
- Ikke kategorisert Solis
- Ikke kategorisert DJI
- Ikke kategorisert Snom
- Ikke kategorisert McIntosh
- Ikke kategorisert One For All
- Ikke kategorisert Caple
- Ikke kategorisert SereneLife
- Ikke kategorisert Turbosound
- Ikke kategorisert Behringer
- Ikke kategorisert Roesle
- Ikke kategorisert APSystems
- Ikke kategorisert Sony
- Ikke kategorisert GoGEN
- Ikke kategorisert Nitecore
- Ikke kategorisert Create
- Ikke kategorisert Furrion
- Ikke kategorisert Glorious
- Ikke kategorisert Pro-Ject
- Ikke kategorisert Yamaha
- Ikke kategorisert Xiaomi
- Ikke kategorisert Venom
- Ikke kategorisert Morel
- Ikke kategorisert Kichler
- Ikke kategorisert Topex
- Ikke kategorisert SMART Technologies
- Ikke kategorisert Trust
- Ikke kategorisert Morphy Richards
- Ikke kategorisert Newstar
- Ikke kategorisert Legrand
- Ikke kategorisert Integral LED
- Ikke kategorisert Lutec
- Ikke kategorisert Vello
- Ikke kategorisert Asus
- Ikke kategorisert Cudy
- Ikke kategorisert Midea
- Ikke kategorisert SBS
- Ikke kategorisert Hayter
- Ikke kategorisert BlueBuilt
- Ikke kategorisert Eufy
- Ikke kategorisert Gys
- Ikke kategorisert Conair
- Ikke kategorisert Turmix
- Ikke kategorisert Franke
- Ikke kategorisert Husqvarna
- Ikke kategorisert Sauber
- Ikke kategorisert Candy
- Ikke kategorisert Shimano
- Ikke kategorisert Axis
- Ikke kategorisert Liebherr
- Ikke kategorisert Carson
- Ikke kategorisert Gourmetmaxx
- Ikke kategorisert Viking
- Ikke kategorisert Gembird
- Ikke kategorisert Truelife
- Ikke kategorisert AkYtec
- Ikke kategorisert ETA
- Ikke kategorisert Voltcraft
- Ikke kategorisert Axor
- Ikke kategorisert Duravit
- Ikke kategorisert Karran
- Ikke kategorisert Elkay
- Ikke kategorisert Brennenstuhl
- Ikke kategorisert Extron
- Ikke kategorisert Lindy
- Ikke kategorisert HP
- Ikke kategorisert HiLook
- Ikke kategorisert Aputure
- Ikke kategorisert Netgear
- Ikke kategorisert BaByliss
- Ikke kategorisert Honor
- Ikke kategorisert XP-PEN
- Ikke kategorisert Danfoss
- Ikke kategorisert Riccar
- Ikke kategorisert Orbegozo
- Ikke kategorisert Media-tech
- Ikke kategorisert Kuppersbusch
- Ikke kategorisert BOYA
- Ikke kategorisert Pioneer
- Ikke kategorisert NEO Tools
- Ikke kategorisert Gorenje
- Ikke kategorisert Summit
- Ikke kategorisert Accucold
- Ikke kategorisert EarFun
- Ikke kategorisert Gram
- Ikke kategorisert WarmlyYours
- Ikke kategorisert Gemini
- Ikke kategorisert Somfy
- Ikke kategorisert Lorex
- Ikke kategorisert Ecler
- Ikke kategorisert Roccat
- Ikke kategorisert AudioControl
- Ikke kategorisert Elsner
- Ikke kategorisert Digitus
- Ikke kategorisert Stokke
- Ikke kategorisert Cabasse
- Ikke kategorisert Koenic
- Ikke kategorisert Panasonic
- Ikke kategorisert Rotel
- Ikke kategorisert KEF
- Ikke kategorisert Monogram
- Ikke kategorisert Unicol
- Ikke kategorisert Audio-Technica
- Ikke kategorisert Olimpia Splendid
- Ikke kategorisert Lian Li
- Ikke kategorisert JLab
- Ikke kategorisert Toa
- Ikke kategorisert Knog
- Ikke kategorisert Rega
- Ikke kategorisert Vox
- Ikke kategorisert Mars Gaming
- Ikke kategorisert Metra
- Ikke kategorisert Pyle
- Ikke kategorisert Westinghouse
- Ikke kategorisert Sencor
- Ikke kategorisert Cello
- Ikke kategorisert Lenovo
- Ikke kategorisert Medion
- Ikke kategorisert Noctua
- Ikke kategorisert Klein Tools
- Ikke kategorisert LevelOne
- Ikke kategorisert Shure
- Ikke kategorisert Michael Todd Beauty
- Ikke kategorisert Schneider
- Ikke kategorisert Roland
- Ikke kategorisert OBSBOT
- Ikke kategorisert Epson
- Ikke kategorisert Kluge
- Ikke kategorisert Bobrick
- Ikke kategorisert Martin
- Ikke kategorisert Kanto
- Ikke kategorisert Scott
- Ikke kategorisert Delta
- Ikke kategorisert Kindermann
- Ikke kategorisert Hortus
- Ikke kategorisert Bertazzoni
- Ikke kategorisert Coyote
- Ikke kategorisert Kidde
- Ikke kategorisert Anker
- Ikke kategorisert Growatt
- Ikke kategorisert Nanoleaf
- Ikke kategorisert Stirling
- Ikke kategorisert Mistral
- Ikke kategorisert JVC
- Ikke kategorisert VMV
- Ikke kategorisert S.M.S.L
- Ikke kategorisert Privileg
- Ikke kategorisert MPM
- Ikke kategorisert PeakTech
- Ikke kategorisert Niceboy
- Ikke kategorisert Khind
- Ikke kategorisert Motorola
- Ikke kategorisert EMOS
- Ikke kategorisert CyberPower
- Ikke kategorisert Sharper Image
- Ikke kategorisert Clean Air Optima
- Ikke kategorisert Manfrotto
- Ikke kategorisert Cosatto
- Ikke kategorisert Fluval
- Ikke kategorisert Cleco
- Ikke kategorisert Kicker
- Ikke kategorisert Bauknecht
- Ikke kategorisert Gude
- Ikke kategorisert Auna
- Ikke kategorisert Taurus
- Ikke kategorisert Heatit
- Ikke kategorisert Midland
- Ikke kategorisert Zebra
- Ikke kategorisert Yealink
- Ikke kategorisert Optex
- Ikke kategorisert Frigidaire
- Ikke kategorisert Deye
- Ikke kategorisert Dimplex
- Ikke kategorisert OSD Audio
- Ikke kategorisert Nibe
- Ikke kategorisert Ryobi
- Ikke kategorisert Breville
- Ikke kategorisert Kodak
- Ikke kategorisert Velleman
- Ikke kategorisert Sharkoon
- Ikke kategorisert Laserliner
- Ikke kategorisert Segway
- Ikke kategorisert Cameo
- Ikke kategorisert Casio
- Ikke kategorisert DataVideo
- Ikke kategorisert RGV
- Ikke kategorisert Hendi
- Ikke kategorisert Gamdias
- Ikke kategorisert Concept
- Ikke kategorisert BeamZ
- Ikke kategorisert Livoo
- Ikke kategorisert Guzzanti
- Ikke kategorisert XO
- Ikke kategorisert Steinel
- Ikke kategorisert Bluesound
- Ikke kategorisert Chauvin Arnoux
- Ikke kategorisert Blackstar
- Ikke kategorisert Hertz
- Ikke kategorisert Kenwood
- Ikke kategorisert Cambridge
- Ikke kategorisert Dell
- Ikke kategorisert Ciarra
- Ikke kategorisert Brandson
- Ikke kategorisert Mybeo
- Ikke kategorisert Aplic
- Ikke kategorisert CSL
- Ikke kategorisert Zoom
- Ikke kategorisert Tru Components
- Ikke kategorisert Hitachi
- Ikke kategorisert Fisher Paykel
- Ikke kategorisert Bearware
- Ikke kategorisert Moen
- Ikke kategorisert Fulgor Milano
- Ikke kategorisert Viewsonic
- Ikke kategorisert B-tech
- Ikke kategorisert Hyundai
- Ikke kategorisert Hansgrohe
- Ikke kategorisert Maginon
- Ikke kategorisert Speco Technologies
- Ikke kategorisert Nec
- Ikke kategorisert IFi Audio
- Ikke kategorisert Tripp Lite
- Ikke kategorisert Nevir
- Ikke kategorisert Infiniton
- Ikke kategorisert Sennheiser
- Ikke kategorisert Ag Neovo
- Ikke kategorisert Henry Engineering
- Ikke kategorisert GPO
- Ikke kategorisert Block
- Ikke kategorisert Ufesa
- Ikke kategorisert Milwaukee
- Ikke kategorisert Smart-AVI
- Ikke kategorisert CEEM
- Ikke kategorisert CAME-TV
- Ikke kategorisert A-Designs
- Ikke kategorisert EchoMaster
- Ikke kategorisert Krups
- Ikke kategorisert Crimson
- Ikke kategorisert Elgato
- Ikke kategorisert Corsair
- Ikke kategorisert Generac
- Ikke kategorisert Dahua Technology
- Ikke kategorisert Cambium Networks
- Ikke kategorisert Scarlett
- Ikke kategorisert Advance
- Ikke kategorisert Indesit
- Ikke kategorisert Daikin
- Ikke kategorisert Canon
- Ikke kategorisert Rowenta
- Ikke kategorisert VAIS Technology
- Ikke kategorisert Zephyr
- Ikke kategorisert Kern
- Ikke kategorisert Lincoln Electric
- Ikke kategorisert Taylor
- Ikke kategorisert AXESS
- Ikke kategorisert DAB
- Ikke kategorisert Be Cool
- Ikke kategorisert Bluetti
- Ikke kategorisert Blaupunkt
- Ikke kategorisert Thermaltake
- Ikke kategorisert Artsound
- Ikke kategorisert Simrad
- Ikke kategorisert Nordic Winter
- Ikke kategorisert Master
- Ikke kategorisert NEP
- Ikke kategorisert Cablexpert
- Ikke kategorisert Ansmann
- Ikke kategorisert Røde
- Ikke kategorisert Makita
- Ikke kategorisert Einhell
- Ikke kategorisert Avidsen
- Ikke kategorisert Lewitt
- Ikke kategorisert Anova
- Ikke kategorisert Posiflex
- Ikke kategorisert Planet
- Ikke kategorisert Biostar
- Ikke kategorisert Mitsubishi
- Ikke kategorisert Marshall
- Ikke kategorisert Showtec
- Ikke kategorisert PCE
- Ikke kategorisert Hikvision
- Ikke kategorisert Sitecom
- Ikke kategorisert Navman
- Ikke kategorisert JIMMY
- Ikke kategorisert Equip
- Ikke kategorisert Conceptronic
- Ikke kategorisert Yorkville
- Ikke kategorisert Toro
- Ikke kategorisert Intermatic
- Ikke kategorisert Tower
- Ikke kategorisert MSR
- Ikke kategorisert Entes
- Ikke kategorisert V-Tac
- Ikke kategorisert Salton
- Ikke kategorisert Novation
- Ikke kategorisert Chipolino
- Ikke kategorisert Fezz
- Ikke kategorisert Eden
- Ikke kategorisert Fuxtec
- Ikke kategorisert Graef
- Ikke kategorisert Megasat
- Ikke kategorisert Mikrotik
- Ikke kategorisert Tristar
- Ikke kategorisert Mophie
- Ikke kategorisert Kohler
- Ikke kategorisert Celly
- Ikke kategorisert Metabo
- Ikke kategorisert Jabra
- Ikke kategorisert Belanger
- Ikke kategorisert Cuisinart
- Ikke kategorisert Doepke
- Ikke kategorisert Anton/Bauer
- Ikke kategorisert Acer
- Ikke kategorisert Dometic
- Ikke kategorisert JBL
- Ikke kategorisert Rigol
- Ikke kategorisert Joy-it
- Ikke kategorisert Body Solid
- Ikke kategorisert Infinity
- Ikke kategorisert DeepCool
- Ikke kategorisert Kali Audio
- Ikke kategorisert Chief
- Ikke kategorisert Majority
- Ikke kategorisert Cybex
- Ikke kategorisert Iiyama
- Ikke kategorisert Nedis
- Ikke kategorisert Crock-Pot
- Ikke kategorisert Helix
- Ikke kategorisert Genesis
- Ikke kategorisert Dyson
- Ikke kategorisert SKS
- Ikke kategorisert Elation
- Ikke kategorisert Magmatic
- Ikke kategorisert Supermicro
- Ikke kategorisert Zendure
- Ikke kategorisert Logilink
- Ikke kategorisert Majestic
- Ikke kategorisert Basetech
- Ikke kategorisert Leviton
- Ikke kategorisert Soundstream
- Ikke kategorisert Klipsch
- Ikke kategorisert PAC
- Ikke kategorisert Xaoc
- Ikke kategorisert Eldom
- Ikke kategorisert Fisher And Paykel
- Ikke kategorisert Hohner
- Ikke kategorisert Britax
- Ikke kategorisert Elba
- Ikke kategorisert Steiner
- Ikke kategorisert Vonroc
- Ikke kategorisert Worx
- Ikke kategorisert Brentwood
- Ikke kategorisert Philco
- Ikke kategorisert Bellari
- Ikke kategorisert Gossen Metrawatt
- Ikke kategorisert Rolls
- Ikke kategorisert MSI
- Ikke kategorisert Chauvet
- Ikke kategorisert Ordo
- Ikke kategorisert Ground Zero
- Ikke kategorisert OnePlus
- Ikke kategorisert V7
- Ikke kategorisert Jenn-Air
- Ikke kategorisert CRUX
- Ikke kategorisert Karma
- Ikke kategorisert Ridem
- Ikke kategorisert Glemm
- Ikke kategorisert StarIink
- Ikke kategorisert Prixton
- Ikke kategorisert HomeCraft
- Ikke kategorisert Nostalgia
- Ikke kategorisert GameDay
- Ikke kategorisert X-Lite
- Ikke kategorisert Söll
- Ikke kategorisert Sparkle
- Ikke kategorisert Edouard Rousseau
- Ikke kategorisert Lawn Star
- Ikke kategorisert Caberg
- Ikke kategorisert Exped
- Ikke kategorisert Igloo
- Ikke kategorisert Heusinkveld
- Ikke kategorisert KED
- Ikke kategorisert EPEVER
- Ikke kategorisert Grothe
- Ikke kategorisert Cane Creek
- Ikke kategorisert Swiss Eye
- Ikke kategorisert SilverStone
- Ikke kategorisert Goodis
- Ikke kategorisert Seiko
- Ikke kategorisert TFA
- Ikke kategorisert X Rocker
- Ikke kategorisert Dreame
- Ikke kategorisert Foreo
- Ikke kategorisert Speed-Link
- Ikke kategorisert Tesla
- Ikke kategorisert Aquael
- Ikke kategorisert Renkforce
- Ikke kategorisert Graff
- Ikke kategorisert Klarstein
- Ikke kategorisert Lauten Audio
- Ikke kategorisert Toddy
- Ikke kategorisert Lexivon
- Ikke kategorisert Icy Dock
- Ikke kategorisert Elta
- Ikke kategorisert ASI
- Ikke kategorisert Gurari
- Ikke kategorisert Varia
- Ikke kategorisert SPL
- Ikke kategorisert I-Tec
- Ikke kategorisert Xigmatek
- Ikke kategorisert Storcube
- Ikke kategorisert Tracer
- Ikke kategorisert Shark
- Ikke kategorisert REMKO
- Ikke kategorisert Phanteks
- Ikke kategorisert EnOcean
- Ikke kategorisert EK Water Blocks
- Ikke kategorisert Hoymiles
- Ikke kategorisert Envertech
- Ikke kategorisert Cougar
- Ikke kategorisert Asrock
- Ikke kategorisert Bestron
- Ikke kategorisert Audiotec Fischer
- Ikke kategorisert PCE Instruments
- Ikke kategorisert Dedra
- Ikke kategorisert Furman
- Ikke kategorisert Abac
- Ikke kategorisert Cata
- Ikke kategorisert Vivax
- Ikke kategorisert Black Diamond
- Ikke kategorisert Advantech
- Ikke kategorisert Stanley
- Ikke kategorisert QSC
- Ikke kategorisert Bitspower
- Ikke kategorisert Black And Decker
- Ikke kategorisert Weston
- Ikke kategorisert Sauter
- Ikke kategorisert WHD
- Ikke kategorisert Schuberth
- Ikke kategorisert Q Acoustics
- Ikke kategorisert Scotsman
- Ikke kategorisert Plantronics
- Ikke kategorisert Proctor Silex
- Ikke kategorisert Radial Engineering
- Ikke kategorisert Karcher
- Ikke kategorisert Orion
- Ikke kategorisert A-NeuVideo
- Ikke kategorisert Beem
- Ikke kategorisert Atlona
- Ikke kategorisert EZ Dupe
- Ikke kategorisert Becken
- Ikke kategorisert I-PRO
- Ikke kategorisert DVDO
- Ikke kategorisert GoXtreme
- Ikke kategorisert Primacoustic
- Ikke kategorisert Avanti
- Ikke kategorisert Acros
- Ikke kategorisert Phil And Teds
- Ikke kategorisert Jotul
- Ikke kategorisert Thermarest
- Ikke kategorisert Powerplus
- Ikke kategorisert Ozito
- Ikke kategorisert Vivanco
- Ikke kategorisert TC Electronic
- Ikke kategorisert Suzuki
- Ikke kategorisert Bionaire
- Ikke kategorisert Huslog
- Ikke kategorisert Glem Gas
- Ikke kategorisert Apogee
- Ikke kategorisert Atomos
- Ikke kategorisert IOptron
- Ikke kategorisert Palmer
- Ikke kategorisert R-Go Tools
- Ikke kategorisert Drayton
- Ikke kategorisert Spektrum
- Ikke kategorisert Jung
- Ikke kategorisert Götze & Jensen
- Ikke kategorisert Native Instruments
- Ikke kategorisert Homedics
- Ikke kategorisert Xvive
- Ikke kategorisert True
- Ikke kategorisert AMX
- Ikke kategorisert Perlick
- Ikke kategorisert Uniden
- Ikke kategorisert Peavey
- Ikke kategorisert BenQ
- Ikke kategorisert Princess
- Ikke kategorisert FOX ESS
- Ikke kategorisert Waterstone
- Ikke kategorisert Mr Steam
- Ikke kategorisert Crown
- Ikke kategorisert DCS
- Ikke kategorisert Fresh N Rebel
- Ikke kategorisert DuroStar
- Ikke kategorisert Duromax
- Ikke kategorisert Owon
- Ikke kategorisert REVITIVE
- Ikke kategorisert Fosi Audio
- Ikke kategorisert Europalms
- Ikke kategorisert Nikon
- Ikke kategorisert HMD
- Ikke kategorisert Sven
- Ikke kategorisert Global Water
- Ikke kategorisert Hamilton Beach
- Ikke kategorisert Extech
- Ikke kategorisert Gaggia
- Ikke kategorisert Tunturi
- Ikke kategorisert Craftsman
- Ikke kategorisert SAVS
- Ikke kategorisert Hansa
- Ikke kategorisert Gastronoma
- Ikke kategorisert Lumens
- Ikke kategorisert Brizo
- Ikke kategorisert Xinfrared
- Ikke kategorisert Getac
- Ikke kategorisert ProLights
- Ikke kategorisert Phonak
- Ikke kategorisert Cherub
- Ikke kategorisert Luxul
- Ikke kategorisert Aruba
- Ikke kategorisert WiiM
- Ikke kategorisert Thor
- Ikke kategorisert Laurastar
- Ikke kategorisert Ambiano
- Ikke kategorisert Horizon
- Ikke kategorisert Bissell
- Ikke kategorisert Antelope Audio
- Ikke kategorisert ESYLUX
- Ikke kategorisert Austral
- Ikke kategorisert Y-brush
- Ikke kategorisert LiveU
- Ikke kategorisert RF-Links
- Ikke kategorisert Fortinge
- Ikke kategorisert Mercury
- Ikke kategorisert Vaddio
- Ikke kategorisert InFocus
- Ikke kategorisert Stinger
- Ikke kategorisert NEXTO DI
- Ikke kategorisert Abus
- Ikke kategorisert AV Tool
- Ikke kategorisert Adventure Kings
- Ikke kategorisert EQ Acoustics
- Ikke kategorisert Michigan
- Ikke kategorisert Vent-A-Hood
- Ikke kategorisert Audix
- Ikke kategorisert Vizio
- Ikke kategorisert Livarno Lux
- Ikke kategorisert Grillmeister
- Ikke kategorisert Ernesto
- Ikke kategorisert Neno
- Ikke kategorisert Rommelsbacher
- Ikke kategorisert One Control
- Ikke kategorisert Bome
- Ikke kategorisert Redback Technologies
- Ikke kategorisert ESX
- Ikke kategorisert City Theatrical
- Ikke kategorisert Omnitronic
- Ikke kategorisert Reber
- Ikke kategorisert Kaiser Nienhaus
- Ikke kategorisert Crestron
- Ikke kategorisert Eurolite
- Ikke kategorisert Manhattan
- Ikke kategorisert Miniland
- Ikke kategorisert Xavax
- Ikke kategorisert MOZA
- Ikke kategorisert Rocstor
- Ikke kategorisert Eureka
- Ikke kategorisert Cruz
- Ikke kategorisert Newland
- Ikke kategorisert Casalux
- Ikke kategorisert Edimax
- Ikke kategorisert Dragonshock
- Ikke kategorisert Russound
- Ikke kategorisert Adj
- Ikke kategorisert Olivetti
- Ikke kategorisert EVOLVEO
- Ikke kategorisert Stadler Form
- Ikke kategorisert Techno Line
- Ikke kategorisert MEE Audio
- Ikke kategorisert Wolfcraft
- Ikke kategorisert Monacor
- Ikke kategorisert Heinner
- Ikke kategorisert Minolta
- Ikke kategorisert Sena
- Ikke kategorisert Innoliving
- Ikke kategorisert Active Era
- Ikke kategorisert Aqara
- Ikke kategorisert POGS
- Ikke kategorisert Beghelli
- Ikke kategorisert BodyCraft
- Ikke kategorisert Superrollo
- Ikke kategorisert Mx Onda
- Ikke kategorisert Koolatron
- Ikke kategorisert Coca-Cola
- Ikke kategorisert Bixolon
- Ikke kategorisert Maruyama
- Ikke kategorisert Bravilor Bonamat
- Ikke kategorisert Kenmore
- Ikke kategorisert Hilti
- Ikke kategorisert D-Jix
- Ikke kategorisert Black Hydra
- Ikke kategorisert I.safe Mobile
- Ikke kategorisert Electro-Voice
- Ikke kategorisert Nimbus
- Ikke kategorisert Lowrance
- Ikke kategorisert Proscan
- Ikke kategorisert Roxio
- Ikke kategorisert Meireles
- Ikke kategorisert Accsoon
- Ikke kategorisert Inspire
- Ikke kategorisert Sebo
- Ikke kategorisert Wharfedale
- Ikke kategorisert Boss
- Ikke kategorisert Tannoy
- Ikke kategorisert Prompter People
- Ikke kategorisert JL Audio
- Ikke kategorisert Edesa
- Ikke kategorisert IOIO
- Ikke kategorisert Genexis
- Ikke kategorisert Buzz Rack
- Ikke kategorisert ZKTeco
- Ikke kategorisert Giordani
- Ikke kategorisert Cadel
- Ikke kategorisert Dualit
- Ikke kategorisert Atlas Sound
- Ikke kategorisert Solo
- Ikke kategorisert Realme
- Ikke kategorisert Wagner
- Ikke kategorisert Ariete
- Ikke kategorisert Bluestork
- Ikke kategorisert Davis
- Ikke kategorisert Comica
- Ikke kategorisert AddLiving
- Ikke kategorisert Melitta
- Ikke kategorisert Constructa
- Ikke kategorisert Lowell
- Ikke kategorisert INOGENI
- Ikke kategorisert Nearity
- Ikke kategorisert Kiloview
- Ikke kategorisert Middle Atlantic
- Ikke kategorisert Mount-It!
- Ikke kategorisert Morley
- Ikke kategorisert Ampeg
- Ikke kategorisert Apantac
- Ikke kategorisert Carry-on
- Ikke kategorisert Liftmaster
- Ikke kategorisert GVision
- Ikke kategorisert IPGARD
- Ikke kategorisert Murideo
- Ikke kategorisert TK Audio
- Ikke kategorisert Rosco
- Ikke kategorisert Proaim
- Ikke kategorisert Cisco
- Ikke kategorisert CGV
- Ikke kategorisert Vacmaster
- Ikke kategorisert Elmo
- Ikke kategorisert Libec
- Ikke kategorisert Point Source Audio
- Ikke kategorisert Macally
- Ikke kategorisert Linhof
- Ikke kategorisert Ade
- Ikke kategorisert MooreCo
- Ikke kategorisert Di4
- Ikke kategorisert Mellerware
- Ikke kategorisert Zenec
- Ikke kategorisert Silver Cross
- Ikke kategorisert Allen & Heath
- Ikke kategorisert American DJ
- Ikke kategorisert AJA
- Ikke kategorisert Postium
- Ikke kategorisert EXO
- Ikke kategorisert RME
- Ikke kategorisert SurgeX
- Ikke kategorisert Alcon
- Ikke kategorisert Vantec
- Ikke kategorisert Silverline
- Ikke kategorisert VAVA
- Ikke kategorisert Tefal
- Ikke kategorisert Vicoustic
- Ikke kategorisert LERAN
- Ikke kategorisert Doffler
- Ikke kategorisert Novy
- Ikke kategorisert Profoto
- Ikke kategorisert TensCare
- Ikke kategorisert Scanstrut
- Ikke kategorisert Mad Dog
- Ikke kategorisert Industrial Music Electronics
- Ikke kategorisert Source Audio
- Ikke kategorisert Black Lion Audio
- Ikke kategorisert Wiha
- Ikke kategorisert Puls Dimension
- Ikke kategorisert Wasp
- Ikke kategorisert OSEE
- Ikke kategorisert Gamewright
- Ikke kategorisert ISDT
- Ikke kategorisert Ilve
- Ikke kategorisert Scosche
- Ikke kategorisert Reolink
- Ikke kategorisert Bebob
- Ikke kategorisert Ashly
- Ikke kategorisert Claypaky
- Ikke kategorisert Premier Mounts
- Ikke kategorisert MuxLab
- Ikke kategorisert Icy Box
- Ikke kategorisert Holosun
- Ikke kategorisert Seagate
- Ikke kategorisert Holzmann
- Ikke kategorisert Blackmagic Design
- Ikke kategorisert Audiolab
- Ikke kategorisert Lectrosonics
- Ikke kategorisert Gravity
- Ikke kategorisert Modbap Modular
- Ikke kategorisert Ikan
- Ikke kategorisert Genius
- Ikke kategorisert Silvercrest
- Ikke kategorisert Rommer
- Ikke kategorisert Traeger
- Ikke kategorisert Memphis Audio
- Ikke kategorisert Focal
- Ikke kategorisert Belkin
- Ikke kategorisert BDI
- Ikke kategorisert Alpine
- Ikke kategorisert Ring
- Ikke kategorisert TC Helicon
- Ikke kategorisert TomTom
- Ikke kategorisert XGIMI
- Ikke kategorisert Omron
- Ikke kategorisert Celestron
- Ikke kategorisert Gymform
- Ikke kategorisert Glide Gear
- Ikke kategorisert Oppo
- Ikke kategorisert Chicco
- Ikke kategorisert AVM
- Ikke kategorisert Impact
- Ikke kategorisert Pelco
- Ikke kategorisert FoxFury
- Ikke kategorisert Argoclima
- Ikke kategorisert Mammut
- Ikke kategorisert Huawei
- Ikke kategorisert Escort
- Ikke kategorisert Heritage Audio
- Ikke kategorisert Safco
- Ikke kategorisert Monoprice
- Ikke kategorisert Stabila
- Ikke kategorisert CTA Digital
- Ikke kategorisert Olight
- Ikke kategorisert Primo
- Ikke kategorisert HammerSmith
- Ikke kategorisert Cyrus
- Ikke kategorisert Steelbody
- Ikke kategorisert Ltech
- Ikke kategorisert Ventev
- Ikke kategorisert HMS Premium
- Ikke kategorisert Elektrobock
- Ikke kategorisert Triton
- Ikke kategorisert Trisa
- Ikke kategorisert Corberó
- Ikke kategorisert AENO
- Ikke kategorisert Korg
- Ikke kategorisert Atosa
- Ikke kategorisert STANDIVARIUS
- Ikke kategorisert Avteq
- Ikke kategorisert Techly
- Ikke kategorisert Izzy
- Ikke kategorisert PureLink
- Ikke kategorisert BirdDog
- Ikke kategorisert UNYKAch
- Ikke kategorisert TeachLogic
- Ikke kategorisert Al-ko
- Ikke kategorisert ADATA
- Ikke kategorisert Mobotix
- Ikke kategorisert Kramer
- Ikke kategorisert ATen
- Ikke kategorisert Blustream
- Ikke kategorisert Laserworld
- Ikke kategorisert Genelec
- Ikke kategorisert Kunft
- Ikke kategorisert Milesight
- Ikke kategorisert Honda
- Ikke kategorisert Spanninga
- Ikke kategorisert Perel
- Ikke kategorisert Bialetti
- Ikke kategorisert Xlyne
- Ikke kategorisert Plant Craft
- Ikke kategorisert Sungrow
- Ikke kategorisert Grundfos
- Ikke kategorisert Bazooka
- Ikke kategorisert Carlsbro
- Ikke kategorisert MoFi
- Ikke kategorisert Blackburn
- Ikke kategorisert Mtx Audio
- Ikke kategorisert Bang And Olufsen
- Ikke kategorisert Delta Dore
- Ikke kategorisert Sole Fitness
- Ikke kategorisert Cowon
- Ikke kategorisert Bebe Confort
- Ikke kategorisert WHALE
- Ikke kategorisert Stalco
- Ikke kategorisert Bunn
- Ikke kategorisert Horizon Fitness
- Ikke kategorisert Cobra
- Ikke kategorisert Sonel
- Ikke kategorisert Lamax
- Ikke kategorisert Jilong
- Ikke kategorisert Maytronics
- Ikke kategorisert Tempmate
- Ikke kategorisert Idec
- Ikke kategorisert Analog Way
- Ikke kategorisert Gamesir
- Ikke kategorisert ZyXEL
- Ikke kategorisert Vogue
- Ikke kategorisert Frilec
- Ikke kategorisert Yaesu
- Ikke kategorisert Concept2
- Ikke kategorisert Musical Fidelity
- Ikke kategorisert Flir
- Ikke kategorisert Rademacher
- Ikke kategorisert NGS
- Ikke kategorisert CTOUCH
- Ikke kategorisert Girmi
- Ikke kategorisert Auray
- Ikke kategorisert RCF
- Ikke kategorisert KJB Security Products
- Ikke kategorisert Harvia
- Ikke kategorisert Microchip
- Ikke kategorisert Homematic IP
- Ikke kategorisert Tektronix
- Ikke kategorisert WilTec
- Ikke kategorisert Easypix
- Ikke kategorisert LC-Power
- Ikke kategorisert SVS
- Ikke kategorisert 8BitDo
- Ikke kategorisert Pardini
- Ikke kategorisert Audeze
- Ikke kategorisert Be Quiet!
- Ikke kategorisert Ergobaby
- Ikke kategorisert Everdure
- Ikke kategorisert Tams Elektronik
- Ikke kategorisert Insta360
- Ikke kategorisert Fieldmann
- Ikke kategorisert Alpen Kreuzer
- Ikke kategorisert Xplora
- Ikke kategorisert H.Koenig
- Ikke kategorisert Wimberley
- Ikke kategorisert Playtive
- Ikke kategorisert Vimar
- Ikke kategorisert Osprey
- Ikke kategorisert Hosa
- Ikke kategorisert Havis
- Ikke kategorisert Daewoo
- Ikke kategorisert Emerson
- Ikke kategorisert Weasy
- Ikke kategorisert Biltema
- Ikke kategorisert Waves
- Ikke kategorisert Bogen
- Ikke kategorisert Electro Harmonix
- Ikke kategorisert Vocopro
- Ikke kategorisert Chrome-Q
- Ikke kategorisert Galaxy Audio
- Ikke kategorisert Altman
- Ikke kategorisert Aiphone
- Ikke kategorisert Atlas
- Ikke kategorisert Graco
- Ikke kategorisert Manta
- Ikke kategorisert MARTOR
- Ikke kategorisert Mean Well
- Ikke kategorisert Exelpet
- Ikke kategorisert Trendnet
- Ikke kategorisert G-Technology
- Ikke kategorisert CubuSynth
- Ikke kategorisert Simpson
- Ikke kategorisert Infasecure
- Ikke kategorisert SecureSafe
- Ikke kategorisert Intellinet
- Ikke kategorisert Hikoki
- Ikke kategorisert Emerio
- Ikke kategorisert Prime3
- Ikke kategorisert OBH Nordica
- Ikke kategorisert Butler
- Ikke kategorisert Duronic
- Ikke kategorisert AVer
- Ikke kategorisert IK Multimedia
- Ikke kategorisert Vankyo
- Ikke kategorisert Murr Elektronik
- Ikke kategorisert TDK-Lambda
- Ikke kategorisert Vitek
- Ikke kategorisert Quantum
- Ikke kategorisert Texas
- Ikke kategorisert Reloop
- Ikke kategorisert ProfiCook
- Ikke kategorisert Arovec
- Ikke kategorisert Harman Kardon
- Ikke kategorisert ARRI
- Ikke kategorisert Acti
- Ikke kategorisert GMB Gaming
- Ikke kategorisert Eurom
- Ikke kategorisert Cadac
- Ikke kategorisert Olympia
- Ikke kategorisert Osram
- Ikke kategorisert Patching Panda
- Ikke kategorisert Consul
- Ikke kategorisert Draytek
- Ikke kategorisert Manitowoc
- Ikke kategorisert Joranalogue
- Ikke kategorisert Klavis
- Ikke kategorisert HyperX
- Ikke kategorisert KDK
- Ikke kategorisert Zhiyun
- Ikke kategorisert ChamSys
- Ikke kategorisert Creative
- Ikke kategorisert OneTouch
- Ikke kategorisert Kospel
- Ikke kategorisert Crosscall
- Ikke kategorisert Dynacord
- Ikke kategorisert Rapoo
- Ikke kategorisert Suunto
- Ikke kategorisert Roidmi
- Ikke kategorisert Aconatic
- Ikke kategorisert IOGEAR
- Ikke kategorisert Ferguson
- Ikke kategorisert DAP Audio
- Ikke kategorisert Artecta
- Ikke kategorisert WyreStorm
- Ikke kategorisert IBEAM
- Ikke kategorisert ToughTested
- Ikke kategorisert Mattel
- Ikke kategorisert Baby Jogger
- Ikke kategorisert Savio
- Ikke kategorisert Healthy Choice
- Ikke kategorisert Yato
- Ikke kategorisert Lund
- Ikke kategorisert Oromed
- Ikke kategorisert Acefast
- Ikke kategorisert Porter-Cable
- Ikke kategorisert Christmas Time
- Ikke kategorisert Barazza
- Ikke kategorisert Chacon
- Ikke kategorisert Marmitek
- Ikke kategorisert Thermador
- Ikke kategorisert Dehner
- Ikke kategorisert Seaward
- Ikke kategorisert Eliminator Lighting
- Ikke kategorisert NordicTrack
- Ikke kategorisert OWC
- Ikke kategorisert Meopta
- Ikke kategorisert Microboards
- Ikke kategorisert CEDAR
- Ikke kategorisert Konica Minolta
- Ikke kategorisert Intel
- Ikke kategorisert Logitech
- Ikke kategorisert Kopul
- Ikke kategorisert KanexPro
- Ikke kategorisert Key Digital
- Ikke kategorisert JoeCo
- Ikke kategorisert BZBGear
- Ikke kategorisert Fiilex
- Ikke kategorisert Gen Energy
- Ikke kategorisert DEERSYNC
- Ikke kategorisert Cranborne Audio
- Ikke kategorisert ChyTV
- Ikke kategorisert Bresser
- Ikke kategorisert Arkon
- Ikke kategorisert Apollo Design
- Ikke kategorisert InLine
- Ikke kategorisert Ardes
- Ikke kategorisert Tactical Fiber Systems
- Ikke kategorisert Telmax
- Ikke kategorisert Sonifex
- Ikke kategorisert Blanco
- Ikke kategorisert ARC
- Ikke kategorisert Grasslin
- Ikke kategorisert Orbis
- Ikke kategorisert Fantini Cosmi
- Ikke kategorisert Theben
- Ikke kategorisert Carel
- Ikke kategorisert Computherm
- Ikke kategorisert Carrier
- Ikke kategorisert Cardo
- Ikke kategorisert President
- Ikke kategorisert Galcon
- Ikke kategorisert K&M
- Ikke kategorisert Xcellon
- Ikke kategorisert Trijicon
- Ikke kategorisert Vortex
- Ikke kategorisert Vertex
- Ikke kategorisert PTZ Optics
- Ikke kategorisert Sescom
- Ikke kategorisert Robus
- Ikke kategorisert Revic
- Ikke kategorisert Panamax
- Ikke kategorisert Kahayan
- Ikke kategorisert Nureva
- Ikke kategorisert Pawa
- Ikke kategorisert Princeton Tec
- Ikke kategorisert ColorKey
- Ikke kategorisert Stamina
- Ikke kategorisert Ideal
- Ikke kategorisert Continental Edison
- Ikke kategorisert Lemair
- Ikke kategorisert Leica
- Ikke kategorisert Soundsphere
- Ikke kategorisert BSS Audio
- Ikke kategorisert Core SWX
- Ikke kategorisert DBX
- Ikke kategorisert Titanwolf
- Ikke kategorisert Perfect Christmas
- Ikke kategorisert Medicinalis
- Ikke kategorisert Uplink
- Ikke kategorisert Rupert Neve Designs
- Ikke kategorisert Crosley
- Ikke kategorisert GPX
- Ikke kategorisert Flama
- Ikke kategorisert Thorens
- Ikke kategorisert Microair
- Ikke kategorisert XCell
- Ikke kategorisert Tepro
- Ikke kategorisert Traco Power
- Ikke kategorisert HK Audio
- Ikke kategorisert Yellow Garden Line
- Ikke kategorisert Chandler
- Ikke kategorisert Singer
- Ikke kategorisert Vogels
- Ikke kategorisert Microsoft
- Ikke kategorisert Newline
- Ikke kategorisert Physa
- Ikke kategorisert Phoenix Gold
- Ikke kategorisert Pitsos
- Ikke kategorisert MBM
- Ikke kategorisert Oricom
- Ikke kategorisert Casablanca
- Ikke kategorisert Lionelo
- Ikke kategorisert Steinberg
- Ikke kategorisert Liam&Daan
- Ikke kategorisert Primewire
- Ikke kategorisert Rittal
- Ikke kategorisert Snow Joe
- Ikke kategorisert Strong
- Ikke kategorisert Universal Audio
- Ikke kategorisert Esatto
- Ikke kategorisert Soundmaster
- Ikke kategorisert Casa Deco
- Ikke kategorisert Adventuridge
- Ikke kategorisert Antec
- Ikke kategorisert Nutrichef
- Ikke kategorisert Parkside
- Ikke kategorisert DPM
- Ikke kategorisert Inverx
- Ikke kategorisert Ugreen
- Ikke kategorisert Haeger
- Ikke kategorisert Cleanmaxx
- Ikke kategorisert Sogo
- Ikke kategorisert Victrola
- Ikke kategorisert Google
- Ikke kategorisert Gloria
- Ikke kategorisert EAT
- Ikke kategorisert Vincent
- Ikke kategorisert Ernitec
- Ikke kategorisert Emko
- Ikke kategorisert Jinbei
- Ikke kategorisert JennAir
- Ikke kategorisert Interstuhl
- Ikke kategorisert Wachendorff
- Ikke kategorisert Astro
- Ikke kategorisert Geneva
- Ikke kategorisert Alfatron
- Ikke kategorisert Indiana Line
- Ikke kategorisert Graphite
- Ikke kategorisert Rockford Fosgate
- Ikke kategorisert Yamazen
- Ikke kategorisert Lantus
- Ikke kategorisert Sumiko
- Ikke kategorisert Chamberlain
- Ikke kategorisert Enders
- Ikke kategorisert Walrus Audio
- Ikke kategorisert Govee
- Ikke kategorisert On-Stage
- Ikke kategorisert Nuki
- Ikke kategorisert HiFi ROSE
- Ikke kategorisert Beautiful
- Ikke kategorisert Foscam
- Ikke kategorisert Ambient Weather
- Ikke kategorisert Gra-Vue
- Ikke kategorisert Enhance
- Ikke kategorisert Digitalinx
- Ikke kategorisert Easyrig
- Ikke kategorisert Bolt
- Ikke kategorisert Steelseries
- Ikke kategorisert Comprehensive
- Ikke kategorisert Ocean Way Audio
- Ikke kategorisert Ocean Matrix
- Ikke kategorisert Peerless-AV
- Ikke kategorisert Blomberg
- Ikke kategorisert Dobot
- Ikke kategorisert Magnus
- Ikke kategorisert Deaf Bonce
- Ikke kategorisert Easymaxx
- Ikke kategorisert Christmaxx
- Ikke kategorisert Fiio
- Ikke kategorisert PreSonus
- Ikke kategorisert Multibrackets
- Ikke kategorisert Evenflo
- Ikke kategorisert ADDAC System
- Ikke kategorisert FBT
- Ikke kategorisert Primera
- Ikke kategorisert Hecate
- Ikke kategorisert Nokia
- Ikke kategorisert Alutruss
- Ikke kategorisert LightZone
- Ikke kategorisert Nacon
- Ikke kategorisert Peak Design
- Ikke kategorisert AVPro Edge
- Ikke kategorisert Blizzard
- Ikke kategorisert Drawmer
- Ikke kategorisert Transparent
- Ikke kategorisert Ergotools Pattfield
- Ikke kategorisert ESE
- Ikke kategorisert Eura
- Ikke kategorisert OKAY
- Ikke kategorisert Uniropa
- Ikke kategorisert Edelkrone
- Ikke kategorisert IHome
- Ikke kategorisert JMAZ Lighting
- Ikke kategorisert GeoVision
- Ikke kategorisert AEA
- Ikke kategorisert NightStick
- Ikke kategorisert JK Audio
- Ikke kategorisert Sabrent
- Ikke kategorisert MIOPS
- Ikke kategorisert Rotatrim
- Ikke kategorisert Defender
- Ikke kategorisert Enttec
- Ikke kategorisert Robinhood
- Ikke kategorisert GVM
- Ikke kategorisert Feelworld
- Ikke kategorisert Eller
- Ikke kategorisert Arthur Martin
- Ikke kategorisert Soundcraft
- Ikke kategorisert Martin Logan
- Ikke kategorisert Hawke
- Ikke kategorisert Andover
- Ikke kategorisert Fortinet
- Ikke kategorisert Prestigio
- Ikke kategorisert Watson
- Ikke kategorisert Grimm Audio
- Ikke kategorisert Deity
- Ikke kategorisert CMI
- Ikke kategorisert Synco
- Ikke kategorisert Betty Bossi
- Ikke kategorisert AVMATRIX
- Ikke kategorisert Lanaform
- Ikke kategorisert Moulinex
- Ikke kategorisert Kubo
- Ikke kategorisert Merging
- Ikke kategorisert Livington
- Ikke kategorisert Akai
- Ikke kategorisert AirTurn
- Ikke kategorisert CAD Audio
- Ikke kategorisert Altrad
- Ikke kategorisert New Pol
- Ikke kategorisert Expressive E
- Ikke kategorisert Amazfit
- Ikke kategorisert Warmup
- Ikke kategorisert EQ-3
- Ikke kategorisert Westfalia
- Ikke kategorisert Oregon Scientific
- Ikke kategorisert Fibaro
- Ikke kategorisert Muller
- Ikke kategorisert Hager
- Ikke kategorisert Stiebel Eltron
- Ikke kategorisert Astralpool
- Ikke kategorisert JANDY
- Ikke kategorisert Zodiac
- Ikke kategorisert Nivona
- Ikke kategorisert Zanussi
- Ikke kategorisert Giardino
- Ikke kategorisert Mutec
- Ikke kategorisert Flycam
- Ikke kategorisert Digigram
- Ikke kategorisert SureFire
- Ikke kategorisert Senal
- Ikke kategorisert Tempo
- Ikke kategorisert Proviel
- Ikke kategorisert Kathrein
- Ikke kategorisert Mafell
- Ikke kategorisert Zelmer
- Ikke kategorisert Autel
- Ikke kategorisert Aspes
- Ikke kategorisert HQ Power
- Ikke kategorisert Velbus
- Ikke kategorisert STANDARD
- Ikke kategorisert BigBlue
- Ikke kategorisert RC Allen
- Ikke kategorisert Plastkon
- Ikke kategorisert Neutrik
- Ikke kategorisert Aquasure
- Ikke kategorisert Triplett
- Ikke kategorisert Bowflex
- Ikke kategorisert Kino Flo
- Ikke kategorisert SmallRig
- Ikke kategorisert Cateye
- Ikke kategorisert Genie
- Ikke kategorisert Soler & Palau
- Ikke kategorisert Ednet
- Ikke kategorisert Tesseract Modular
- Ikke kategorisert Thule
- Ikke kategorisert Burg-Wachter
- Ikke kategorisert Stelton
- Ikke kategorisert Bora
- Ikke kategorisert Bavaria
- Ikke kategorisert Medela
- Ikke kategorisert AVerMedia
- Ikke kategorisert Minox
- Ikke kategorisert Maxxmee
- Ikke kategorisert Propellerhead
- Ikke kategorisert Auer Signal
- Ikke kategorisert Nilfisk
- Ikke kategorisert Wiesenfield
- Ikke kategorisert Sun Joe
- Ikke kategorisert Bulgin
- Ikke kategorisert Black Decker
- Ikke kategorisert ART
- Ikke kategorisert Toolland
- Ikke kategorisert Zipper
- Ikke kategorisert Inkbird
- Ikke kategorisert Beemoo
- Ikke kategorisert Klark Teknik
- Ikke kategorisert Hotone
- Ikke kategorisert Clatronic
- Ikke kategorisert Shimbol
- Ikke kategorisert Hedbox
- Ikke kategorisert Tele Vue
- Ikke kategorisert Atdec
- Ikke kategorisert Honey-Can-Do
- Ikke kategorisert Think Tank
- Ikke kategorisert Phonic
- Ikke kategorisert Ultimate Support
- Ikke kategorisert Gabor
- Ikke kategorisert Sôlt
- Ikke kategorisert EGO
- Ikke kategorisert Fellowes
- Ikke kategorisert Ferplast
- Ikke kategorisert Bushnell
- Ikke kategorisert Cooler Master
- Ikke kategorisert Olympus
- Ikke kategorisert AV:link
- Ikke kategorisert Pure 100
- Ikke kategorisert Hirschmann
- Ikke kategorisert Interphone
- Ikke kategorisert Kernau
- Ikke kategorisert Hanseatic
- Ikke kategorisert Proline
- Ikke kategorisert Xblitz
- Ikke kategorisert Hozelock
- Ikke kategorisert Sime
- Ikke kategorisert NovaStar
- Ikke kategorisert Petite Chérie
- Ikke kategorisert Taga Harmony
- Ikke kategorisert ACCU-CHEK
- Ikke kategorisert SoundTube
- Ikke kategorisert Njoy
- Ikke kategorisert Studio Titan
- Ikke kategorisert EOTech
- Ikke kategorisert AstrHori
- Ikke kategorisert Icron
- Ikke kategorisert Pyrex
- Ikke kategorisert NUX
- Ikke kategorisert Angler
- Ikke kategorisert James
- Ikke kategorisert Ebro
- Ikke kategorisert Visage
- Ikke kategorisert Geemarc
- Ikke kategorisert Ruark Audio
- Ikke kategorisert Platypus
- Ikke kategorisert DEHN
- Ikke kategorisert Koenig
- Ikke kategorisert Trezor
- Ikke kategorisert Raya
- Ikke kategorisert EtherWAN
- Ikke kategorisert ClearOne
- Ikke kategorisert Aqua-Vu
- Ikke kategorisert Ferrofish
- Ikke kategorisert HPRC
- Ikke kategorisert Dracast
- Ikke kategorisert Really Right Stuff
- Ikke kategorisert Decimator
- Ikke kategorisert Chimera
- Ikke kategorisert Eartec
- Ikke kategorisert Devialet
- Ikke kategorisert ButtKicker
- Ikke kategorisert Pliant Technologies
- Ikke kategorisert Blonder Tongue
- Ikke kategorisert ZWO
- Ikke kategorisert MEPROLIGHT
- Ikke kategorisert Antelope
- Ikke kategorisert Crystal Video
- Ikke kategorisert Vixen
- Ikke kategorisert Avenview
- Ikke kategorisert Tilta
- Ikke kategorisert Futaba
- Ikke kategorisert Luxli
- Ikke kategorisert Hawk-Woods
- Ikke kategorisert SWIT
- Ikke kategorisert PAG
- Ikke kategorisert Simeo
- Ikke kategorisert Lenco
- Ikke kategorisert Testboy
- Ikke kategorisert Baby Lock
- Ikke kategorisert Senseca
- Ikke kategorisert NeoMounts
- Ikke kategorisert MJX
- Ikke kategorisert Western Co.
- Ikke kategorisert WEG
- Ikke kategorisert ProFlo
- Ikke kategorisert Rohl
- Ikke kategorisert Vivolink
- Ikke kategorisert Protector
- Ikke kategorisert Allibert
- Ikke kategorisert IDIS
- Ikke kategorisert Marklin
- Ikke kategorisert RTS
- Ikke kategorisert Nebula
- Ikke kategorisert Gardenline
- Ikke kategorisert KeepOut
- Ikke kategorisert Dexibell
- Ikke kategorisert Hecht
- Ikke kategorisert LAS
- Ikke kategorisert Ruggard
- Ikke kategorisert Elvid
- Ikke kategorisert ICE Watch
- Ikke kategorisert OM SYSTEM
- Ikke kategorisert Neumann
- Ikke kategorisert OpenVox
- Ikke kategorisert POLARIS
- Ikke kategorisert 4ms
- Ikke kategorisert Hobart
- Ikke kategorisert JAYS
- Ikke kategorisert Moman
- Ikke kategorisert DiversiTech
- Ikke kategorisert Aukey
- Ikke kategorisert Violectric
- Ikke kategorisert Aalberg Audio
- Ikke kategorisert Rollei
- Ikke kategorisert Bugaboo
- Ikke kategorisert Tascam
- Ikke kategorisert Evooch
- Ikke kategorisert Pontec
- Ikke kategorisert Godrej
- Ikke kategorisert Mooer
- Ikke kategorisert M-Audio
- Ikke kategorisert Bolin Technology
- Ikke kategorisert Rexing
- Ikke kategorisert Total Chef
- Ikke kategorisert Aduro
- Ikke kategorisert Ambrogio
- Ikke kategorisert Williams Sound
- Ikke kategorisert Total
- Ikke kategorisert PoLabs
- Ikke kategorisert Astell&Kern
- Ikke kategorisert Taiji
- Ikke kategorisert Futurelight
- Ikke kategorisert Dali
- Ikke kategorisert Suntec
- Ikke kategorisert Metronic
- Ikke kategorisert COLBOR
- Ikke kategorisert Berker
- Ikke kategorisert Tornado
- Ikke kategorisert AOpen
- Ikke kategorisert Digi-Pas
- Ikke kategorisert Marshall Electronics
- Ikke kategorisert Grace Design
- Ikke kategorisert Golden Age Project
- Ikke kategorisert Umidigi
- Ikke kategorisert Pfister
- Ikke kategorisert InfiRay
- Ikke kategorisert Arduino
- Ikke kategorisert Fellow
- Ikke kategorisert Engel
- Ikke kategorisert Elbe
- Ikke kategorisert Kolcraft
- Ikke kategorisert SKROSS
- Ikke kategorisert Trace Elliot
- Ikke kategorisert Klauke
- Ikke kategorisert Tiger
- Ikke kategorisert Equator
- Ikke kategorisert Axler
- Ikke kategorisert Lazer
- Ikke kategorisert Symmons
- Ikke kategorisert DMT
- Ikke kategorisert Jacuzzi
- Ikke kategorisert Gioteck
- Ikke kategorisert Gerber
- Ikke kategorisert Royale
- Ikke kategorisert Z CAM
- Ikke kategorisert Pentatech
- Ikke kategorisert Studiologic
- Ikke kategorisert Hammond
- Ikke kategorisert Ketron
- Ikke kategorisert MGL Avionics
- Ikke kategorisert Dubatti
- Ikke kategorisert Venicci
- Ikke kategorisert Baby Trend
- Ikke kategorisert Adder
- Ikke kategorisert Inglesina
- Ikke kategorisert Fito
- Ikke kategorisert Lucide
- Ikke kategorisert Urbanista
- Ikke kategorisert Cherry
- Ikke kategorisert GolfBuddy
- Ikke kategorisert Lotus
- Ikke kategorisert Das Keyboard
- Ikke kategorisert Schaffner
- Ikke kategorisert Vitec
- Ikke kategorisert Technaxx
- Ikke kategorisert Nicols
- Ikke kategorisert Jane
- Ikke kategorisert Mercusys
- Ikke kategorisert Hamlet
- Ikke kategorisert Revlon
- Ikke kategorisert Wallas
- Ikke kategorisert ARNOLD Lichttechnik
- Ikke kategorisert Legamaster
- Ikke kategorisert Onkyo
- Ikke kategorisert Matterport
- Ikke kategorisert AZZA
- Ikke kategorisert API Audio
- Ikke kategorisert Atlantis Land
- Ikke kategorisert Bestway
- Ikke kategorisert Beurer
- Ikke kategorisert Moomin
- Ikke kategorisert Belulu
- Ikke kategorisert YSI
- Ikke kategorisert Jedo
- Ikke kategorisert RIX
- Ikke kategorisert Bayco
- Ikke kategorisert Wilson
- Ikke kategorisert Ionmax
- Ikke kategorisert Creality
- Ikke kategorisert Compex
- Ikke kategorisert Crelando
- Ikke kategorisert Algo
- Ikke kategorisert Dinstar
- Ikke kategorisert FeiyuTech
- Ikke kategorisert EMeet
- Ikke kategorisert Motrona
- Ikke kategorisert CaterRacks
- Ikke kategorisert Sedona
- Ikke kategorisert Uniross
- Ikke kategorisert Akasa
- Ikke kategorisert Perixx
- Ikke kategorisert Noordi
- Ikke kategorisert Globalo
- Ikke kategorisert SwitchBot
- Ikke kategorisert Corona
- Ikke kategorisert Michelin
- Ikke kategorisert Adonit
- Ikke kategorisert Bavaria By Einhell
- Ikke kategorisert Schwinn
- Ikke kategorisert SoundPEATS
- Ikke kategorisert MagnaPool
- Ikke kategorisert Sensiplast
- Ikke kategorisert Krone
- Ikke kategorisert Coors Light
- Ikke kategorisert Konig & Meyer
- Ikke kategorisert Telestar
- Ikke kategorisert Arco
- Ikke kategorisert Brita
- Ikke kategorisert Aguilar
- Ikke kategorisert Exibel
- Ikke kategorisert KoolScapes
- Ikke kategorisert GFM
- Ikke kategorisert Avid
- Ikke kategorisert On-Q
- Ikke kategorisert Parallels
- Ikke kategorisert Arturia
- Ikke kategorisert Thinkware
- Ikke kategorisert Jonard Tools
- Ikke kategorisert Adesso
- Ikke kategorisert Royal Sovereign
- Ikke kategorisert Netter Vibration
- Ikke kategorisert Califone
- Ikke kategorisert Sunding
- Ikke kategorisert Teesa
- Ikke kategorisert Bliss Outdoors
- Ikke kategorisert BeSafe
- Ikke kategorisert Air Guard
- Ikke kategorisert Oase
- Ikke kategorisert Phoenix Contact
- Ikke kategorisert Elcom
- Ikke kategorisert DEXP
- Ikke kategorisert Geuther
- Ikke kategorisert Platinum
- Ikke kategorisert Petkit
- Ikke kategorisert Rainbow
- Ikke kategorisert Lenoxx
- Ikke kategorisert Martin Audio
- Ikke kategorisert Hurricane
- Ikke kategorisert Tiptop Audio
- Ikke kategorisert Winix
- Ikke kategorisert GoPro
- Ikke kategorisert Powerfix
- Ikke kategorisert MAAS
- Ikke kategorisert Audibax
- Ikke kategorisert Babysense
- Ikke kategorisert Babyzen
- Ikke kategorisert Aqua Joe
- Ikke kategorisert Mackie
- Ikke kategorisert Medisana
- Ikke kategorisert Line 6
- Ikke kategorisert Dynon Avionics
- Ikke kategorisert Uvex
- Ikke kategorisert Florabest
- Ikke kategorisert Crivit
- Ikke kategorisert Creality3D
- Ikke kategorisert Beaba
- Ikke kategorisert Tork
- Ikke kategorisert Lescha
- Ikke kategorisert Grunkel
- Ikke kategorisert Babymoov
- Ikke kategorisert Lezyne
- Ikke kategorisert Vitalmaxx
- Ikke kategorisert Swissvoice
- Ikke kategorisert Intex
- Ikke kategorisert Joie
- Ikke kategorisert Proficare
- Ikke kategorisert Redrock Micro
- Ikke kategorisert UAvionix
- Ikke kategorisert GW Instek
- Ikke kategorisert Kemo
- Ikke kategorisert Ledger
- Ikke kategorisert LARQ
- Ikke kategorisert Auriol
- Ikke kategorisert Luxman
- Ikke kategorisert InSinkErator
- Ikke kategorisert ORCA
- Ikke kategorisert SSV Works
- Ikke kategorisert Eminent
- Ikke kategorisert Basil
- Ikke kategorisert Swift
- Ikke kategorisert TOTO
- Ikke kategorisert Sonos
- Ikke kategorisert Brilliant
- Ikke kategorisert AcuRite
- Ikke kategorisert Dymo
- Ikke kategorisert YA-MAN
- Ikke kategorisert Doro
- Ikke kategorisert Sonicware
- Ikke kategorisert CRAFT + MAIN
- Ikke kategorisert Roline
- Ikke kategorisert V-Tone
- Ikke kategorisert Hellberg
- Ikke kategorisert HELGI
- Ikke kategorisert Gold Note
- Ikke kategorisert Dual
- Ikke kategorisert Redsbaby
- Ikke kategorisert Hovicon
- Ikke kategorisert Bryton
- Ikke kategorisert Western Digital
- Ikke kategorisert Parasound
- Ikke kategorisert Stelzner
- Ikke kategorisert LightKeeper Pro
- Ikke kategorisert XPG
- Ikke kategorisert BMAX
- Ikke kategorisert Camille Bauer
- Ikke kategorisert Cressi
- Ikke kategorisert DoorBird
- Ikke kategorisert Hacienda
- Ikke kategorisert Singercon
- Ikke kategorisert GoldAir
- Ikke kategorisert Magivaac
- Ikke kategorisert Gem Toys
- Ikke kategorisert Intergas
- Ikke kategorisert Budda
- Ikke kategorisert Paladin
- Ikke kategorisert Pivo
- Ikke kategorisert Sharkbite
- Ikke kategorisert HuddleCamHD
- Ikke kategorisert Anybus
- Ikke kategorisert MAK
- Ikke kategorisert Magnavox
- Ikke kategorisert CatSynth
- Ikke kategorisert (Recovery)
- Ikke kategorisert Crucial
- Ikke kategorisert Echo
- Ikke kategorisert ILive
- Ikke kategorisert Ipevo
- Ikke kategorisert Tineco
- Ikke kategorisert Simplified MFG
- Ikke kategorisert Eero
- Ikke kategorisert Springfree
- Ikke kategorisert Connection
- Ikke kategorisert Technical Pro
- Ikke kategorisert Solplanet
- Ikke kategorisert JOBY
- Ikke kategorisert Crane
- Ikke kategorisert DOD
- Ikke kategorisert Videotel Digital
- Ikke kategorisert Bretford
- Ikke kategorisert Badiona
- Ikke kategorisert Dangerous Music
- Ikke kategorisert Smith-Victor
- Ikke kategorisert Zylight
- Ikke kategorisert Blind Spot
- Ikke kategorisert BIOS Living
- Ikke kategorisert Burris
- Ikke kategorisert TAURUS Titanium
- Ikke kategorisert Millennia
- Ikke kategorisert Sound Devices
- Ikke kategorisert AREXX
- Ikke kategorisert Blue Sky
- Ikke kategorisert 3M
- Ikke kategorisert Rocktrail
- Ikke kategorisert American International
- Ikke kategorisert T-Rex
- Ikke kategorisert Hayward
- Ikke kategorisert Cloud
- Ikke kategorisert Apricorn
- Ikke kategorisert Foster
- Ikke kategorisert PulseAudio
- Ikke kategorisert Mulex
- Ikke kategorisert Comfortisse
- Ikke kategorisert Yphix
- Ikke kategorisert Cricut
- Ikke kategorisert Ember
- Ikke kategorisert Sifflus
- Ikke kategorisert Magliner
- Ikke kategorisert Em-Trak
- Ikke kategorisert Black Box
- Ikke kategorisert Albert Heijn
- Ikke kategorisert Infantino
- Ikke kategorisert Bestgreen
- Ikke kategorisert Empress Effects
- Ikke kategorisert Exagerate
- Ikke kategorisert ACOPower
- Ikke kategorisert AGM
- Ikke kategorisert Hanwha
- Ikke kategorisert Clarion
- Ikke kategorisert Enbrighten
- Ikke kategorisert Audison
- Ikke kategorisert Flame
- Ikke kategorisert Garden Feelings
- Ikke kategorisert UDG Gear
- Ikke kategorisert Lastolite
- Ikke kategorisert Weidmüller
- Ikke kategorisert NANO Modules
- Ikke kategorisert EA Elektro Automatik
- Ikke kategorisert Bahr
- Ikke kategorisert Grand Effects
- Ikke kategorisert Franklin
- Ikke kategorisert Sodapop
- Ikke kategorisert Absco
- Ikke kategorisert Lowepro
- Ikke kategorisert Neumärker
- Ikke kategorisert SunPower
- Ikke kategorisert Black Line
- Ikke kategorisert Dunlop
- Ikke kategorisert Qian
- Ikke kategorisert Aim TTi
- Ikke kategorisert Bbf
- Ikke kategorisert Datapath
- Ikke kategorisert Gima
- Ikke kategorisert Soundskins
- Ikke kategorisert Chord
- Ikke kategorisert Paradigm
- Ikke kategorisert Morphor
- Ikke kategorisert GC Audio
- Ikke kategorisert Advanced Network Devices
- Ikke kategorisert Telycam
- Ikke kategorisert Lynx
- Ikke kategorisert DQ
- Ikke kategorisert Nextorage
- Ikke kategorisert JLCooper
- Ikke kategorisert Buchla & TipTop Audio
- Ikke kategorisert GOgroove
- Ikke kategorisert XTRARM
- Ikke kategorisert Rock N Roller
- Ikke kategorisert OptiTrack
- Ikke kategorisert ZZ-2
- Ikke kategorisert Varta
- Ikke kategorisert Foppapedretti
- Ikke kategorisert Drive Medical
- Ikke kategorisert E-ast
- Ikke kategorisert BMW
- Ikke kategorisert Doona
- Ikke kategorisert Trio Lighting
- Ikke kategorisert Emga
- Ikke kategorisert SolidDrive
- Ikke kategorisert Induction Dynamics
- Ikke kategorisert USL
- Ikke kategorisert ENDORFY
- Ikke kategorisert SKB
- Ikke kategorisert Sangean
- Ikke kategorisert Freewell
- Ikke kategorisert Vivotek
- Ikke kategorisert Vermeiren
- Ikke kategorisert Evolis
- Ikke kategorisert ESI
- Ikke kategorisert Cyber Acoustics
- Ikke kategorisert Sissel
- Ikke kategorisert Matrox
- Ikke kategorisert PUR
- Ikke kategorisert Sonorous
- Ikke kategorisert Troy-Bilt
- Ikke kategorisert Desview
- Ikke kategorisert Audio Pro
- Ikke kategorisert Bright Starts
- Ikke kategorisert IPEGA
- Ikke kategorisert Brändi
- Ikke kategorisert QZ
- Ikke kategorisert MSolutions
- Ikke kategorisert Artrom
- Ikke kategorisert Pigtronix
- Ikke kategorisert Marathon
- Ikke kategorisert Bush
- Ikke kategorisert Unitech
- Ikke kategorisert Targus
- Ikke kategorisert Storm
- Ikke kategorisert ISi
- Ikke kategorisert Nuance
- Ikke kategorisert Cubot
- Ikke kategorisert Helight
- Ikke kategorisert DARTS
- Ikke kategorisert ETON
- Ikke kategorisert Singularity Computers
- Ikke kategorisert Boehringer Ingelheim
- Ikke kategorisert Iluv
- Ikke kategorisert Act
- Ikke kategorisert Sesame Street
- Ikke kategorisert Ingenuity
- Ikke kategorisert Lava
- Ikke kategorisert Digital Forecast
- Ikke kategorisert Autoscript
- Ikke kategorisert GLP
- Ikke kategorisert Longvie
- Ikke kategorisert Xuma
- Ikke kategorisert Ledvance
- Ikke kategorisert Magewell
- Ikke kategorisert Go-eCharger
- Ikke kategorisert IMG Stageline
- Ikke kategorisert BioChef
- Ikke kategorisert SLV
- Ikke kategorisert Mac Tools
- Ikke kategorisert Ergotron
- Ikke kategorisert Goal Zero
- Ikke kategorisert Icon
- Ikke kategorisert InvisibleShield
- Ikke kategorisert Voigtlander
- Ikke kategorisert Hailo
- Ikke kategorisert Nyko
- Ikke kategorisert XD-Design
- Ikke kategorisert Step2
- Ikke kategorisert Gator
- Ikke kategorisert SmartGyro
- Ikke kategorisert Megableu
- Ikke kategorisert Dreamland
- Ikke kategorisert Star Belly
- Ikke kategorisert Pabobo
- Ikke kategorisert Tiny Love
- Ikke kategorisert Needit
- Ikke kategorisert Brabantia
- Ikke kategorisert Nevadent
- Ikke kategorisert Pulsar
- Ikke kategorisert SetonixSynth
- Ikke kategorisert Qu-Bit
- Ikke kategorisert Oras
- Ikke kategorisert Phase Technology
- Ikke kategorisert Casr
- Ikke kategorisert Hypnos
- Ikke kategorisert CkeyiN
- Ikke kategorisert Vulcan
- Ikke kategorisert BlaknBlu
- Ikke kategorisert Louroe Electronics
- Ikke kategorisert Leifheit
- Ikke kategorisert Orbitrek
- Ikke kategorisert Zaahn
- Ikke kategorisert Brinno
- Ikke kategorisert MOOOV
- Ikke kategorisert DB Technologies
- Ikke kategorisert Expobar
- Ikke kategorisert Crem
- Ikke kategorisert Fischer
- Ikke kategorisert Livn
- Ikke kategorisert Kaorka
- Ikke kategorisert Sportime
- Ikke kategorisert Airlive
- Ikke kategorisert Wise
- Ikke kategorisert Quasar Science
- Ikke kategorisert Zeapon
- Ikke kategorisert CLIMAQUA
- Ikke kategorisert Tece
- Ikke kategorisert Keter
- Ikke kategorisert Beltronics
- Ikke kategorisert Sommer
- Ikke kategorisert VOREL
- Ikke kategorisert Lahti Pro
- Ikke kategorisert Nous
- Ikke kategorisert HiRO
- Ikke kategorisert Vantrue
- Ikke kategorisert Elight
- Ikke kategorisert Forodi
- Ikke kategorisert CELLFAST
- Ikke kategorisert MOZOS
- Ikke kategorisert Noise Engineering
- Ikke kategorisert UGo
- Ikke kategorisert Koliber
- Ikke kategorisert Jan Nowak
- Ikke kategorisert RAM Mounts
- Ikke kategorisert Buxton
- Ikke kategorisert Toorx
- Ikke kategorisert Miracle Smile
- Ikke kategorisert Zacuto
- Ikke kategorisert VARI-LITE
- Ikke kategorisert Real Cable
- Ikke kategorisert Syrp
- Ikke kategorisert Adobe
- Ikke kategorisert ViewZ
- Ikke kategorisert IsoTek
- Ikke kategorisert Playseat
- Ikke kategorisert Pengo
- Ikke kategorisert Satco
- Ikke kategorisert Agfa
- Ikke kategorisert Sloan
- Ikke kategorisert Sophos
- Ikke kategorisert Evga
- Ikke kategorisert Racktime
- Ikke kategorisert Videotec
- Ikke kategorisert FABER CASTELL
- Ikke kategorisert Kica
- Ikke kategorisert Humminbird
- Ikke kategorisert Digitech
- Ikke kategorisert PAX
- Ikke kategorisert Moxa
- Ikke kategorisert Sunny
- Ikke kategorisert Sightron
- Ikke kategorisert Simmons
- Ikke kategorisert Woood
- Ikke kategorisert Infosec
- Ikke kategorisert Lowel
- Ikke kategorisert Leba
- Ikke kategorisert Kendall Howard
- Ikke kategorisert Starlight Xpress
- Ikke kategorisert Guide
- Ikke kategorisert Hoffman
- Ikke kategorisert Therm-a-Rest
- Ikke kategorisert Elbro
- Ikke kategorisert Diamond Audio
- Ikke kategorisert Nofred
- Ikke kategorisert Newport Brass
- Ikke kategorisert Ambient
- Ikke kategorisert AudioQuest
Nyeste Ikke kategorisert Manualer

10 April 2025

10 April 2025

10 April 2025

10 April 2025

10 April 2025

10 April 2025

10 April 2025
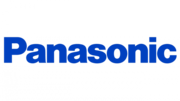
10 April 2025

9 April 2025

9 April 2025